According to different cotton spinning processes, cotton yarn is divided into three types: carded cotton yarn, combed cotton yarn and waste spinning yarn.
The production process of carded cotton yarn is as follows: opening and cleaning cotton - carding - drawing and slitting - roving - spun yarn - post-processing.
The production process of combed cotton yarn: opening and cleaning cotton - combing - combing preparation - combing - drawing - drawing - roving - spun yarn - post-processing.
Waste spinning cotton is made of waste and noil from cotton mills and goes through three processes: cleaning, roller combing, and spinning. The following focuses on the role of each process in the cotton spinning process, focusing on carded cotton yarn and combed cotton yarn.
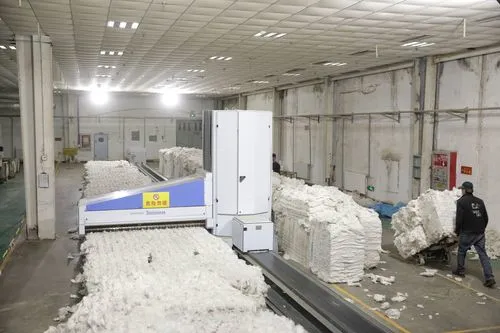
01 Opening and cleaning
Blowing cotton is the first process in cotton spinning. The raw materials fed, whether raw cotton or chemical fiber, are compressed into bales.
Raw cotton contains impurities and chemical fibers contain defects.
- The role of the cotton opening and cleaning process
(1) Opening:
(2) Impurity removal: Effectively remove various impurities and defects in the raw cotton, and reduce the amount of spinnable fibers as much as possible.
(3) Blending: According to the cotton composition, raw cotton with different properties is fully and carefully blended.
(4) Uniform rolling: making cotton rolls of certain specifications and uniformity for use in the carding process.
- The role of a single machine in the opening and cleaning combined unit The above functions are completed by a series of single-machine opening and cleaning combined units. These single machines can be divided into five categories according to their main functions:
(1) Cotton picking machinery
(2) Cotton blending machinery
(4) Cotton feeding machinery
(5) Cotton cleaning machinery
The function of the carding process is:
02 Carding
(1) Combing
(2) Impurity Removal
(3) Even mixing
(4) Strip
03 Combing
Cotton spinning is divided into two types: carded spinning system and combed spinning system. The difference between the latter and the former is that the combing process is added between carding and drawing. The reason for adding the combing process is that there are many short fibers and knots in the carded sliver, and the fiber straightness and separation are also poor. These defects will affect the quality of the yarn. Therefore, when spinning yarns with higher quality requirements, the combed spinning system must be used. Compared with the coarse carded yarn with the same count, the combed yarn after the fine spinning process can increase the yarn strength by 10%~20%, reduce the number of cotton knots and impurities by 50%~60%, and the yarn has uniform dryness and good gloss. Therefore, the combed yarn has the characteristics of high strength, few knots, uniform dryness and good gloss.
- The role of combing process
(1) Eliminate short lint
(2) Eliminate cotton knots and impurities
(3) Straightening parallel fibers
(4) Uniform strip formation
- Composition of the finishing process The combing process includes two parts: combing preparation and combing machine.
(1) Combing preparation
The role of combing preparation is
â‘ Improve the straightening and parallelism of fibers.
â‘¡ Make small rolls with accurate quantity, tight winding, clear layers and uniform cotton layers in the vertical and horizontal directions for use in combing machines.
(2) Combing: Combing is a process using a combing machine.
04 Drawing
Although the raw sliver made by the carding machine has the initial shape of yarn, its long segment unevenness is very large, and most of the fibers are in a hooked or curled state. Therefore, the raw sliver needs to be further processed through the drawing process to improve the quality of the sliver.
The main function of the drawing process is
(1) Merger
(2) Drafting
(3) Mixing
(4) Strip
The draw frame consists of three parts: feeding, drafting and sliver output.
05 Roving
The functions of the roving process are:
(1) Drafting: Stretch the cotton strip 5 to 10 times longer and thinner…
(2) Twisting
(3) Winding
06 Fine yarn
The spinning process is the last process in spinning production. It is to spin the coarse yarn into fine yarn with a certain linear density and in line with national quality standards for twisting, weaving or knitting.
The function of the spinning process is
(1) Drafting
(2) Twisting
(3) Winding
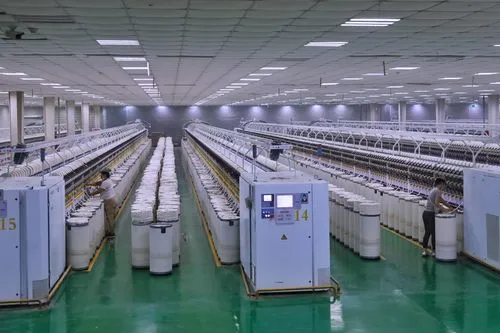
07 Post-processing
The processing after the spinning process is collectively referred to as post-processing, which generally includes winding, doubling, twisting, reeling, and packaging. The finished product is bobbin yarn or hank yarn.
- Winding process
- Yarn doubling process
- Feeding process
- Yarn reeling and packaging